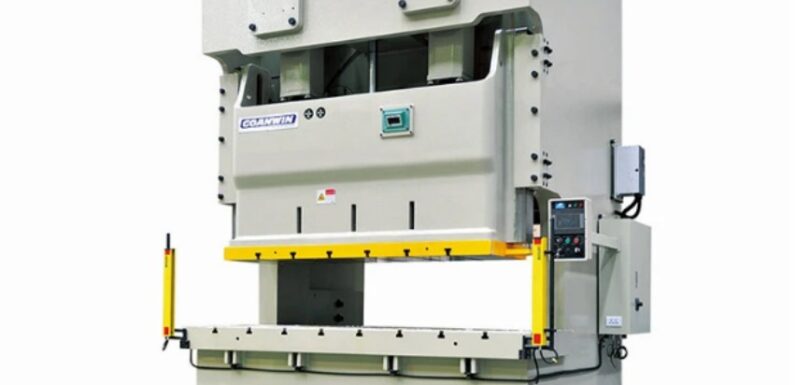
In the realm of manufacturing and industrial production, efficiency is paramount. Every operation seeks to optimize its processes to minimize waste, increase output, and enhance overall productivity. One crucial component in achieving these objectives is the press feeder.
Press feeders play a pivotal role in the metal stamping and forming industry. They are specialized machines designed to automate the feeding of material into a press, ensuring a continuous and uniform supply for the manufacturing process. These feeders come in various types, with servo feeders emerging as a cutting-edge solution for precision and flexibility.
Understanding Press Feeders: A Closer Look
At the core of press feeder technology lies the principle of automation. Traditional press feeders are mechanical devices equipped with rollers or grippers to advance material into the press. These feeders rely on mechanical mechanisms for operation, which can limit their speed and accuracy.
In contrast, servo feeders harness the power of servo motors and advanced control systems to achieve superior performance. By integrating servo technology, these feeders offer precise control over feeding speed, length, and positioning. This level of precision enables manufacturers to meet stringent quality standards and accommodate a diverse range of materials and part geometries.
The Advantages of Servo Feeders
-
Precision and Accuracy
Servo feeders excel in delivering precise and consistent material feeding. The ability to control the servo motor’s speed and position with high accuracy ensures uniformity in the manufacturing process. This precision is particularly valuable in applications where tight tolerances are required, such as automotive and aerospace components.
-
Flexibility and Versatility
Unlike their mechanical counterparts, servo feeders offer unparalleled flexibility. With programmable control systems, manufacturers can easily adjust feed length, speed, and acceleration to suit different production requirements. This versatility enables rapid changeovers between jobs and facilitates the production of diverse part designs without costly retooling.
-
Enhanced Productivity
The combination of precision and flexibility inherent in servo feeders translates to enhanced productivity on the production floor. By minimizing downtime associated with setup changes and ensuring consistent feed rates, these feeders optimize the overall efficiency of the stamping process. As a result, manufacturers can increase throughput and meet customer demands more effectively.
Applications of Press Feeders in Industry
Press feeders find widespread use across various industries, including automotive, electronics, appliances, and consumer goods. These versatile machines play a vital role in manufacturing a wide array of stamped and formed components, ranging from simple brackets to complex assemblies.
In the automotive sector, press feeders are indispensable for producing body panels, chassis components, and structural reinforcements. The precision and reliability of servo feeder make them ideal for stamping intricate parts with tight dimensional tolerances. Moreover, their ability to handle different types of metals and alloys allows automotive manufacturers to meet the diverse requirements of modern vehicle designs.
Optimizing Press Feeder Performance
While press feeders offer numerous benefits, maximizing their performance requires careful consideration of various factors. Proper setup, maintenance, and integration with other equipment are essential for achieving optimal results.
-
Setup and Calibration
During initial setup, it is crucial to calibrate the press feeder to ensure accurate material feeding. This involves configuring the servo motor’s parameters, such as speed, torque, and acceleration, to match the specific requirements of the production process. Additionally, proper alignment of the feeder with the press is essential to prevent misfeeds and ensure smooth operation.
-
Regular Maintenance
Like any mechanical or electrical system, press feeders require regular maintenance to sustain optimal performance. Routine inspections, lubrication of moving parts, and replacement of worn components are vital for preventing breakdowns and extending the equipment’s lifespan. Moreover, periodic calibration and tuning of servo systems help maintain precision and accuracy over time.
-
Integration with Press Controls
Seamless integration between the press feeder and the overall manufacturing system is crucial for achieving efficient operation. Modern press controls offer advanced features such as recipe management, automatic job changeovers, and real-time monitoring of production parameters. By integrating the feeder with these control systems, manufacturers can streamline workflow, minimize manual intervention, and maximize productivity.
Conclusion: Embracing Innovation for Success
In the ever-evolving landscape of manufacturing, the adoption of advanced technologies is imperative for staying competitive. Press feeders, particularly servo feeders, represent a significant advancement in material feeding and stamping processes. Their precision, flexibility, and productivity-enhancing capabilities make them indispensable assets for modern industrial operations.
By understanding the principles and benefits of press feeders, manufacturers can leverage these technologies to optimize their production processes, reduce costs, and deliver high-quality products to market. Whether in automotive, electronics, or other industries, the strategic implementation of press feeders can drive efficiency and innovation, paving the way for sustainable growth and success.