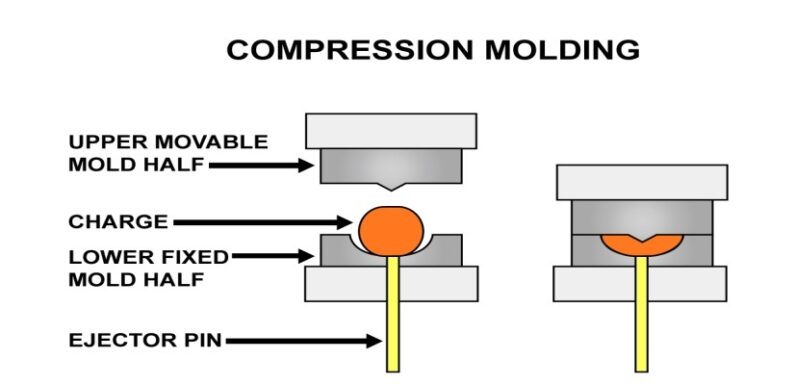
Compression moulding is a widely used manufacturing process that plays a crucial role in the production of durable and complex designs. It is particularly valued in industries such as automotive, aerospace, and consumer goods, where high-strength materials and intricate shapes are essential. This method of moulding involves placing a pre-measured amount of material, typically in the form of a preheated plastic or rubber, into a mould cavity. The mould is then closed, applying heat and pressure to shape the material into the desired design. The process’s versatility and efficiency make it a go-to option for creating parts that must withstand harsh conditions while maintaining precise and intricate features.
How Compression Moulding Works
The compression moulding process begins with the selection of the right material for the product’s needs, such as thermosets, rubbers, or composites. These materials are chosen for their ability to endure high levels of heat and pressure without losing integrity. The selected material is then heated to a molten state or softened enough to flow easily into the mould cavity. A precise amount of material is placed into the mould, and the mould is closed under significant pressure. Heat is then applied to cure or harden the material, forming it into the desired shape. Once the material has cooled and solidified, the mould opens to reveal the finished part.
Advantages of Compression Moulding for Durable Designs
One of the key benefits of compression moulding is its ability to produce durable components. The process ensures that materials such as rubber, thermosetting plastics, and composite materials maintain their integrity under stress, making them ideal for high-performance applications. Compression moulded parts are known for their strength, resistance to wear and tear, and ability to withstand extreme temperatures and environmental conditions. This durability is critical in industries where components are subjected to frequent exposure to heat, chemicals, or mechanical stress, such as in automotive engines, aerospace components, or industrial machinery.
Furthermore, the Compression Moulding process can produce parts with excellent dimensional stability. The heat and pressure applied during the moulding process ensure that the finished product remains consistent in size and shape, even under varying operational conditions. This consistency is essential for components that must fit precisely within larger assemblies or systems.
Compression Moulding and Complex Designs
Compression moulding excels in creating intricate, complex designs that would be difficult or cost-prohibitive to produce using other methods. The ability to produce parts with undercuts, multi-dimensional curves, and complex geometric shapes is a major advantage. Compression moulding can also accommodate a variety of inserts, such as metal components, reinforcing fibers, or special coatings, allowing for enhanced strength or functionality within a single part.The moulding process enables manufacturers to create detailed textures, logos, or patterns on the surface of the component, which can add aesthetic value and increase product functionality
Applications Across Industries
Compression moulding is used in various industries to produce parts that need to meet specific performance requirements. In the automotive industry, components like seals, gaskets, and bushings are created using this method due to their need for both durability and precision. Aerospace also relies on compression moulding to produce lightweight yet strong components that can withstand extreme temperatures and pressures during flight.In consumer goods, compression moulding is used to manufacture items such as electrical insulation, rubber grips, and plastic casings, which benefit from the process’s ability to create durable yet lightweight parts.